Die Mission der Siemens Healthineers ist alles andere als normal oder alltäglich. Die Gesundheitspioniere in Erlangen betreuen Gesundheitsversorger in aller Welt beim Ausbau der Präzisionsmedizin und Optimieren der Patientenbetreuung. Darüber hinaus unterstützen zahlreiche Produkte und Dienstleistungen die Digitalisierung des Gesundheitswesens und das Krankenhausmanagement.
„Hier steht ein aussagekräftiges Statement vom Kunden“
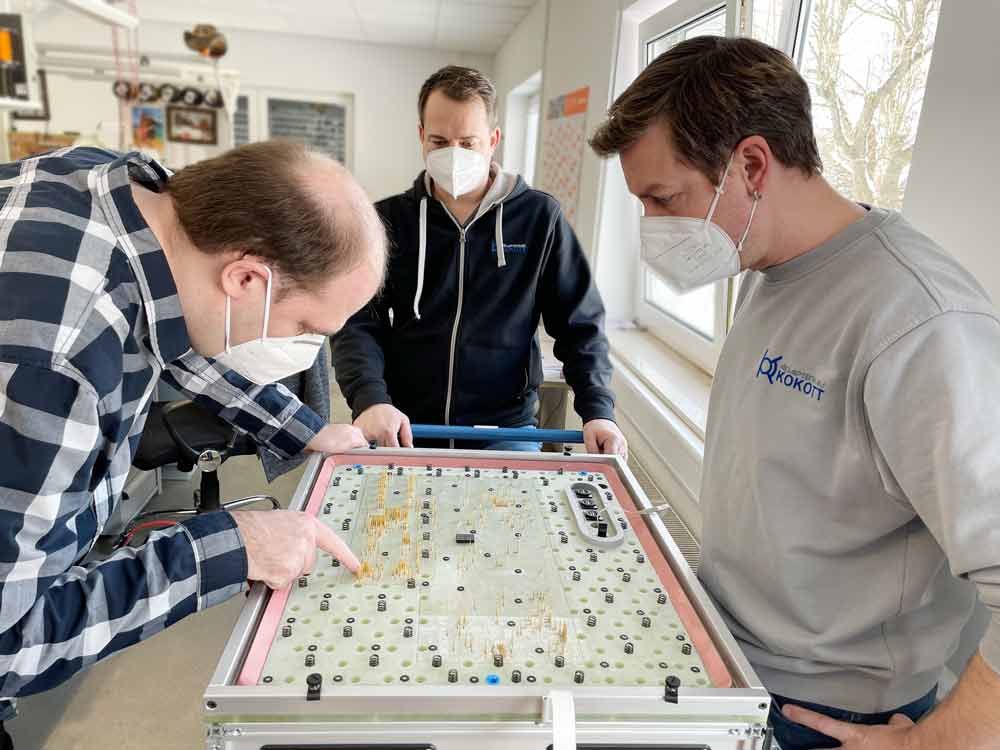
Jeden Tag profitieren etwa fünf Millionen Patienten von Siemens Medizintechnik in den Bereichen diagnostische und therapeutische Bildgebung, Labordiagnostik oder molekulare Medizin. Hierzu sind hochkomplexe Geräte und Medizintechnologien vonnöten, die immer neuen Kundenansprüchen gerecht werden müssen und steigende Konnektivitätsanforderungen für Prüfadapter mit sich bringen.
Der Adapterbau Kokott realisiert bereits seit den 1990er Jahren entsprechende Prüftechnik, um die einwandfreie Funktionalität und Prozessqualität hochsensibler Baukomponenten für modernste Medizinapparate sicherzustellen.
Das jüngste Projekt für Siemens Healthineers war die Anfertigung eines Funktionstest Vakuumadapters zur Prüfung von Baugruppen im Bereich Computer-Tomografie. Wir nutzten den Kundenbesuch, um mehr über die – in mehrfacher Hinsicht – ungewöhnlichen Begleitumstände dieses Sonderauftrags zu erfahren.
Herr Kaiser, wie ist der Auftrag für Siemens Healthineers einzuordnen?
Kaiser: „Zum einen handelt es sich dabei um einen komplexen Funktionstest Vakuumadapter, und noch dazu war es ein Eilauftrag, kurz vor Weihnachten. Die Verdrahtung, wir sprechen hier von über 400 Nadeln, hat Kokott über Weihnachten in Sonderschichten absolviert. Übrigens in Rekordzeit.“
Ist es üblich, dass der Kunde zur Produktabnahme in die Fertigung kommt?
Kaiser: „Bei einfacheren Adaptern ist das meistens nicht nötig. Aber ein größeres Projekt wie dieses, mit vielen Einbauten und einem aufwendigeren Verdrahtungsplan, bei dem es einiges zu beachten gibt, kann ich gleich vor Ort prüfen und ggf. Änderungswünsche einbringen. Das spart viel Zeit.“
Für welchen Einsatzzweck ist der Prüfadapter vorgesehen?
Kaiser: „Wir brauchen den Adapter für qualitativ hochwertige Serientests in der Medizintechnik, zur Prüfung einer Flachbaugruppe, die zentraler Bestandteil einer PET CT-Anlage ist. In diesem Fall handelt es sich um eine Komponente für eine Siemens-Tochter in den USA.“
Sie verantworten bei den Siemens Healthineers Großprojekte in der Digitaltechnik. Inwieweit hat Corona Ihr Business und den Tagesablauf verändert?
Kaiser: „Viele Kollegen arbeiten zurzeit im Home-Office, da wechselt man sich auch ab. Siemens Healthineers ist natürlich systemrelevant, das heißt in der Fertigung geht es normal weiter, nur eben unter Hygienemaßnahmen. Gerade jetzt ist die Diagnose ja sehr wichtig. Wir vertreiben mittlerweile auch ein Covid19
PCR Testsystem für die Labordiagnostik und unsere Computertomographen können bei betroffenen Patienten für das Röntgen der Lungen eingesetzt werden.“
Warum war das Projekt so zeitkritisch? Bekommen Sie in diesem Sektor Bestellungen on Demand?
Kaiser: „Nein, eigentlich nicht. Das Vorgängermodell des Computertomographen läuft aus und die Bauteile sind zudem größtenteils „abgekündigt“. Das heißt, die Teileverfügbarkeit hat ein Enddatum und das Nachfolgeprodukt muss im März nahtlos eingeführt werden. Und da es sich um Baugruppen für ein PET-CT handelt, die auch für Untersuchungen im Rahmen der Covid19-Pandemie dringend gebraucht werden, hatten wir für den Adapter- und Verdrahtungsplan ein sehr sportliches Zeitfenster.“
Wie ist der Ablauf solcher Großprojekte unter normalen Umständen?
Kaiser: „Im Normalfall wird ein Projekt rechtzeitig ausgeschrieben und bei Lieferanten angefragt, dann wird nach Angebot entschieden und losgelegt. Wenn wir Adapter benötigen, für die Kokott seine Stärken ausspielen kann, favorisieren wir Kokott. Sollten die Ressourcen in Schnaittach knapp sein, müssen wir Alternativen finden.“
Welche Faktoren sind in der Regel ausschlaggebend?
Kaiser: „Adapterbau ist Sonderbau mit Einmalkosten, es ist kein preisgetriebenes Business. Qualität, Präzision und absolute Termintreue sind viel wichtiger als ein paar Euro Rabatt. Sehen Sie, ein high-end CT-Gerät kostet über eine Million. Wir liefern für das PET-CT zum Serienstart mit ca. 20 bis 30 Baugruppen pro Monat in die Fertigungsstraße und das muss stabil und zuverlässig laufen.“
Da bleibt vermutlich kaum Zeit zum Ausruhen …
Kaiser: „Fast zeitgleich wird in Abstimmung eines Kollegen ein mechanisch baugleicher ICT Adapter geplant und gebaut, mit noch mehr Nadeln, ca. 1.600 Hülsen und über 2.000 Kontaktierungsbohrungen, die uns dadurch ein nachträgliches manuelles Setzen von Hülsen deutlich erleichtern. Bei Medizingeräten dieser Güte darf es keinen Lieferungsausfall oder Verzug geben. Mit dem Adapter können wir mögliche Fertigungsfehler schneller analysieren und beheben. Ebenso wollen wir in unserer Fertigung stets kontrollieren, ob alles rund läuft. Wenn ein Fehler auftaucht, muss ich wissen: Welches Bauteil ist kaputt? Woher kommt der Fehler?
Der ICT Prüfadapter ermöglicht es Bauteile einzeln zu vermessen. Dann kann man genau sagen, welches Bauteil fehlt oder welcher Messwert z.B. bei passiven Bauelementen außerhalb der Toleranz liegt. Für diese Bauart ist beim Adapterbau dann mehr Fleißarbeit gefragt, weil es weniger Sonderverdrahtungen gibt, dafür viele 1:1-Verdrahtung zu den Schnittstellenblöcken.“
Wie viele solche Prüfadapter haben Sie zu verantworten?
Kaiser: „Für größere Projekte wie dieses, ist man als Test-Ingenieur ein gutes halbes Jahr beschäftigt, dann erst geht es zum nächsten Adapter. Kleinere Adapter kann man in drei bis vier Monaten abhandeln.“
Wie lange arbeiten Sie schon mit Kokott-Adaptern?
Kaiser: „Meinen ersten Adapter habe ich 2011 von Kokott bauen lassen, als ich bei Siemens anfing. Die Kollegen hatten damals bereits gute Erfahrungen mit dem Adapterbau Kokott gemacht. Manche Adapter sind schon 30 Jahre im Betrieb, die Zusammenarbeit besteht also schon länger.“
Sicher kennen Sie alle relevanten Adapterbauer in Deutschland. Gibt es etwas, das Sie an Kokott besonders schätzen
Kaiser: „Zum einen hat Kokott einen großen Standortvorteil, dadurch dass sie in der Nähe sind, gerade einmal 26 km von unserem Headquarter in Erlangen entfernt. Aber im Grunde hebt sich Kokott vor allem dadurch ab, dass unsere Ansprechpartner ein komplettes Verständnis für den Adapterbau haben, dass sie sich mit einem Projekt beschäftigen, sich einlesen und das Gesamtkonzept des Adapters verstehen. Sie machen es einfach am besten. Wir können die Lieferanten ja zum Glück danach auswählen, wo es am besten gelöst wird. Und wo man gute Erfahrungen macht, da geht man wieder hin, logisch.“
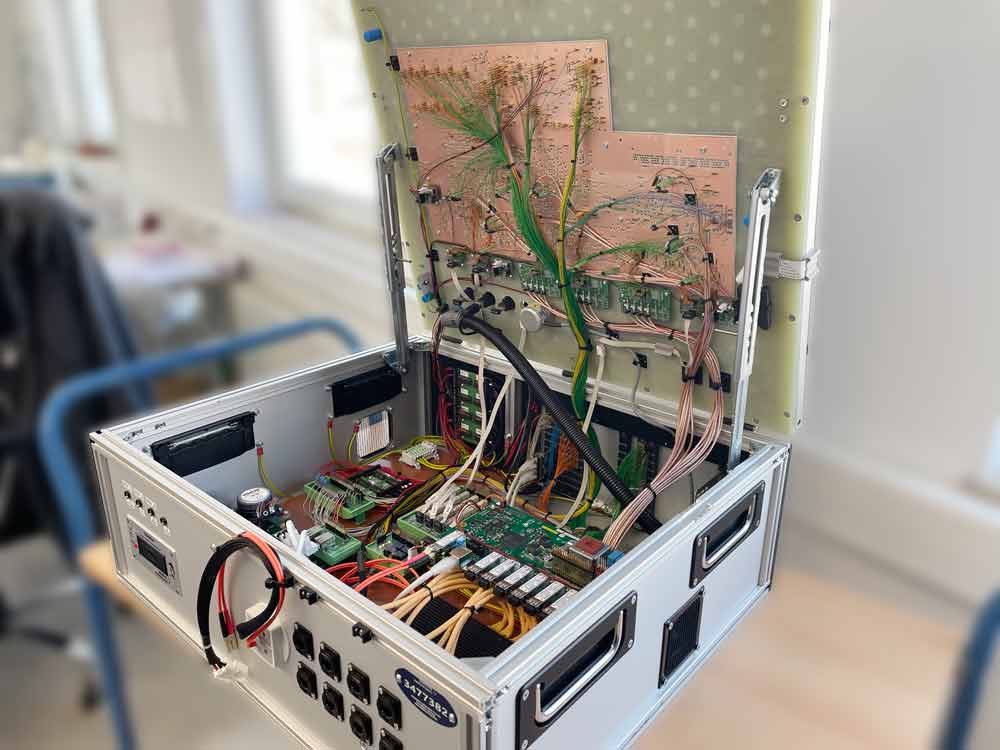
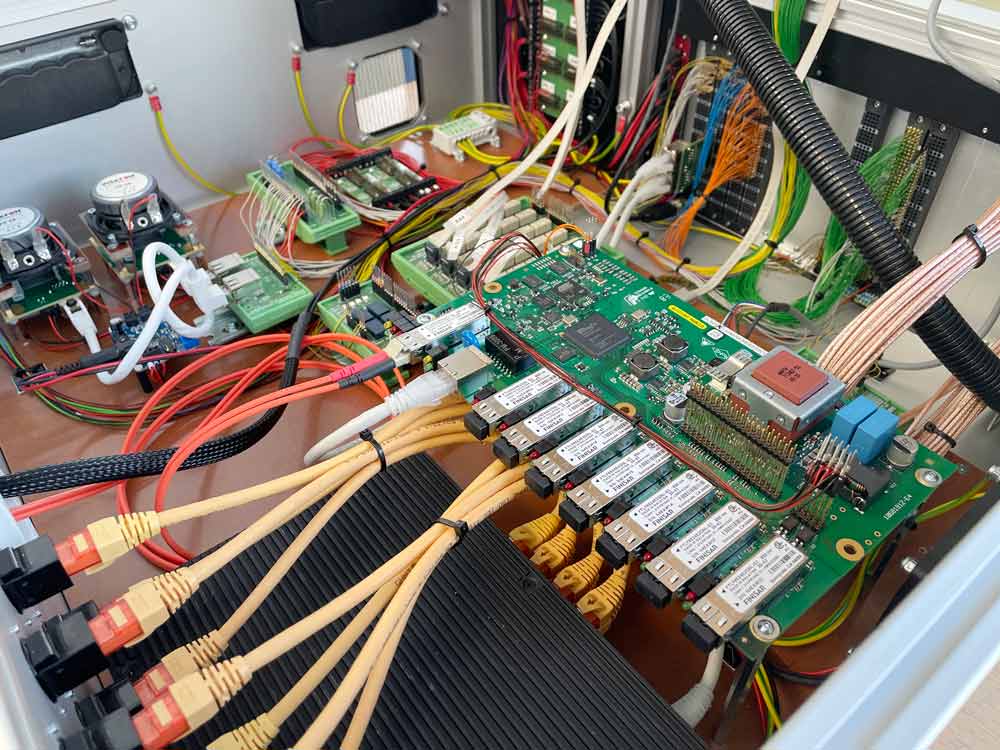
Adapter-Kennzahlen
- Typ: Funktionstest (FCT) / Vakuumadapter, einstufig im leichten Alu-Case.
- Mehr als 400 Sonderverdrahtete Nadeln, ca. 2.000 Kontaktierungsbohrungen.
- Geringes Gewicht, robuste Bauart, lange Verfügbarkeit (bis zu 10 Jahre).
- Aufgabe: Funktionsprüfung einer Baugruppe für ein PET Computertomographen des US-amerikanischen Geschäftsbereichs Molecular Imaging.
- Wartungsarbeiten sind nach ca. 5.000 Hüben vorgesehen.
Über Siemens Healthineers
- Global Player im Gesundheitswesen.
- Seit 120 Jahren Pionier im Gesundheitswesen.
- 7.500 Mitarbeiter am Standort Erlangen.
- Produkte & Services: Medizinische Bildgebung, Labordiagnostik, Point-of-Care-Diagnostik, Healthcare-IT, Klinische Lösungen & Indikationen.
- https://www.siemens-healthineers.com/de